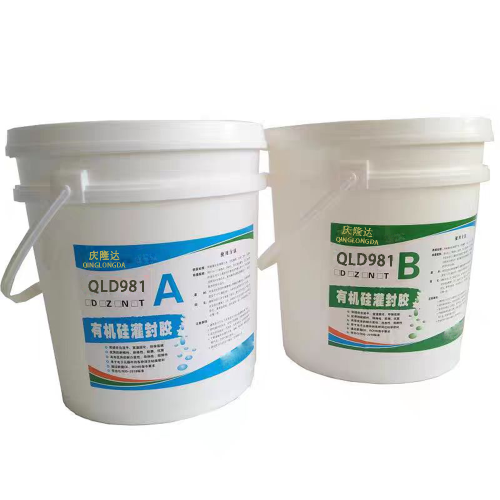
Two-component encapsulating system based on polyurethane
Product Description:
This two-component polyurethane encapsulant offers exceptional hardness, making it an ideal choice for protecting sensitive electronic components from impact and environmental factors. With its durable construction, it creates a tough, long-lasting barrier that shields delicate circuitry from moisture, dust, and other contaminants. The high-quality materials used ensure reliable performance, even in demanding applications. Whether youre working on industrial equipment or consumer electronics, this encapsulant provides the robust protection you need to safeguard your valuable components. Its ease of application and curing process make it a convenient solution for streamlining your production workflow.
981 polyurethane encapsulant
It is used for potting various electronic components such as precision capacitors. It has high hardness after curing, and is a good material to replace epoxy resin. Vacuum degassing and heating equipment is required.
982 polyurethane encapsulant
It is used for potting and bonding of precision lightning arresters, various transformers, transformers, filters, control boards, igniters, etc.
983 polyurethane encapsulant
General-purpose type, suitable for potting all kinds of electronic products.
984 polyurethane encapsulant
It has excellent elasticity and toughness, can be repaired, has excellent electrical properties, and can replace silicone potting compound.
985 Polyurethane Adhesive:
Semi-flowing, used for bonding and sealing electronic components.
Performance parameters:
Performance indicators |
981 |
982 |
983 |
984 |
985 |
Color |
White/Yellow |
White/Yellow |
White/Yellow |
White/Yellow |
White/Yellow |
Viscosity, (mpa.s,A/B) |
5000~8000/300~380 |
Half-flowing |
|||
Viscosity of mixture (mpa.s) |
3000~5000 |
Half-flowing |
|||
Operation time,mins (min) |
≤30 |
30~45 |
45~60 |
45~60 |
30~60 |
Initial curing time (h) |
3~5 |
5~7 |
8~10 |
8~10 |
3~6 |
Full curing time (h) |
24 |
36 |
48 |
48 |
24 |
Hardness, (shore A/D) |
≥80D |
80±10A |
60±10A |
40±10A |
80±10A |
Thread shrinkage (%) |
0.3 |
||||
Density,,g/cm3, 25℃ (g/cm3) |
1.5~1.7 |
||||
Application temperature, (℃) |
-60~150 |
||||
Dielectric strength, (kV/mm, 25℃) |
≥25 |
||||
Volume resistivity (Ω·cm,25℃) |
1.0×1015 |
||||
Thermal conductivity (W/M·K) |
≥0.6 |
||||
Shear strength (MPa) |
≥3.5 |
≥2.3 |
≥1.5 |
≥0.8 |
≥4.5 |
Attributes and Application:
Two-component, room temperature curing, hardness adjustable polyurethane material, good fluidity, room temperature curing, cured into elastic rubber. It has excellent high and low temperature resistance, hydrolysis stability and excellent insulation properties. The potted electrical parts have a variety of functions such as fixing, insulation, heat dissipation, explosion-proof, and confidentiality. It is suitable for all kinds of pouring bonding and sealing of electronic components such as high-pressure, high-frequency, damp-hot environments and underwater instruments and meters.
Processing:
1. Clean up the potting place, no oil, no water, no debris.
2. Weigh the A and B components according to the ratio, put them in the mixing tank, stir fully and mix evenly (do not stir the air into the glue when stirring). It is best to vacuum and degasser for about 5 minutes, and the amount of glue should not exceed 1/2 of the container, otherwise the glue will overflow during degassing.
3. Slowly pour the mixed rubber into the device to be potted. In winter construction work, if the ambient temperature is lower than 5 °C, it is best to preheat the A and B components to about 15 °C.
4. The potted workpiece is cured at room temperature, and the surface can only enter the next process after drying, and it takes 1 day to completely cure. In summer, the temperature is high, and the curing will be faster; In winter, when the temperature is low, the curing will be slower.
Notes:
1. If component A is placed for a long time and there is precipitation or stratification, it should be stirred evenly before use; Component B is easy to crystallize at low temperature, and should be placed in a higher temperature room in advance to dissolve without affecting the performance of the product.
2. The mixed glue should be used up at one time, and the unused A and B components should be sealed and stored separately.
3. Sealed and stored in a cool and dry place for six months.